Selecting the Right Double-Sided Tape for Foam Application: A Guide to Prevent Cracking Issues
Introduction
In various industries, foam is widely used as a versatile material for cushioning, insulation, and packaging purposes. To ensure the durability and effectiveness of foam products, it is crucial to select the appropriate double-sided tape for adhesion. This article aims to provide a comprehensive guide on selecting the right double-sided tape for foam applications, focusing on preventing cracking issues during use.
Factors to Consider When Selecting Double-Sided Tape for Foam Applications
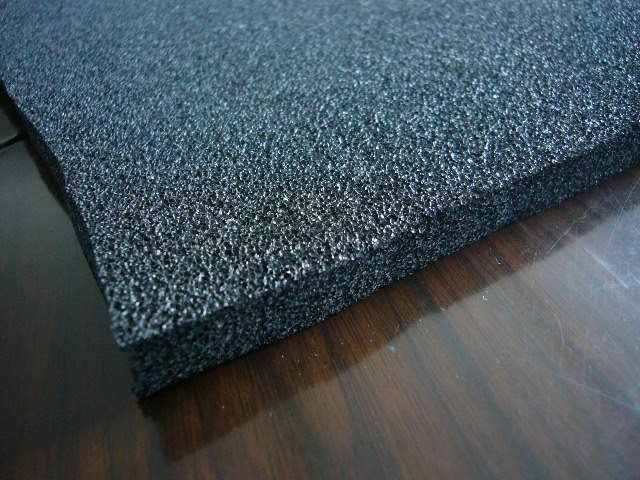
Adhesive Type
There are two main types of adhesives used in double-sided tapes: acrylic and rubber. Acrylic adhesives are known for their high initial tack and quick bonding, while rubber adhesives offer better durability and heat resistance. Depending on the specific application and environmental conditions, choose the appropriate adhesive type for your foam product.
Adhesive Strength
Adhesive strength is measured in terms of bonding power and holding capacity. For foam applications, it is essential to select a double-sided tape with sufficient adhesive strength to ensure a secure bond between the foam and the substrate.
Temperature Resistance
The temperature resistance of the double-sided tape is crucial, especially when the foam product is exposed to varying temperatures. Choose a tape with a suitable temperature range that can withstand the expected operating conditions without compromising the bond.
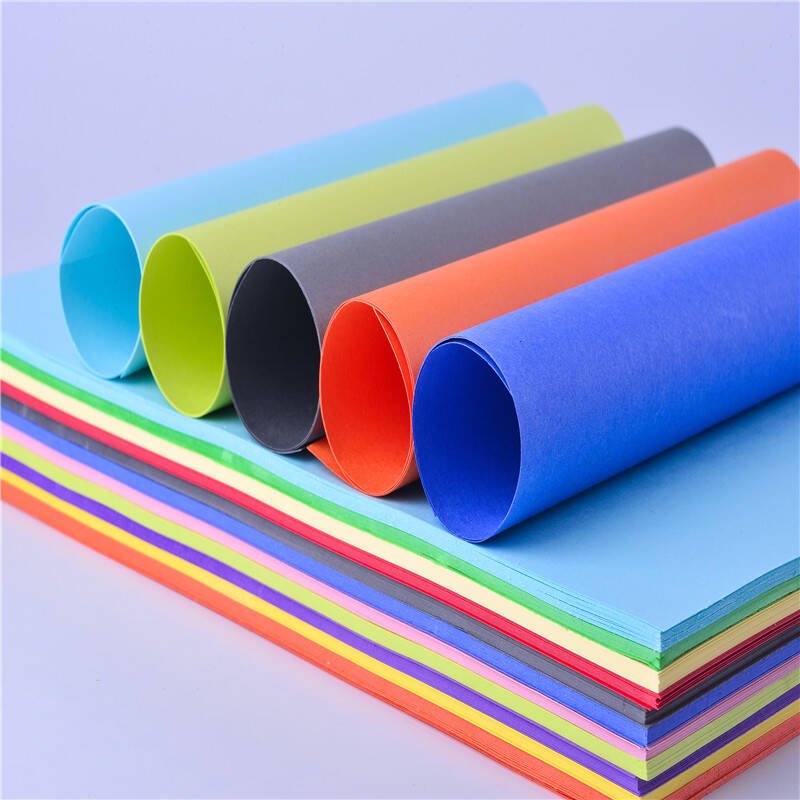
Tape Thickness
The thickness of the double-sided tape can affect the overall performance of the foam product. A thicker tape may provide better shock absorption, while a thinner tape may offer a more discreet and lightweight solution. Consider the specific requirements of your application when selecting the appropriate tape thickness.
Tape Width
The width of the double-sided tape should be chosen based on the size and shape of the foam product. A wider tape may be necessary for larger or irregularly shaped foam pieces, while a narrower tape may be suitable for smaller or intricate applications.
Release Liner
The release liner is the protective layer that covers the adhesive side of the double-sided tape. It is essential to choose a release liner that is easy to remove without damaging the foam or leaving residue behind.
Tips for Preventing Cracking Issues in Foam Applications
Clean Surfaces
Before applying the double-sided tape, ensure that both the foam and the substrate surfaces are clean and free of dirt, dust, and other contaminants. This will help to create a strong bond and prevent cracking issues.
Apply Even Pressure
When attaching the foam to the substrate, apply even pressure to ensure a consistent bond throughout the surface area. Uneven pressure may cause the tape to stretch, leading to cracking or delamination.
Allow Proper Curing Time
After applying the double-sided tape, allow sufficient time for the adhesive to cure and develop its full bonding strength. Rushing the curing process may result in a weaker bond and increased risk of cracking.
Avoid Excessive Heat and Humidity
Exposure to extreme heat and humidity can weaken the bond between the foam and the substrate, leading to cracking issues. When possible, store and use foam products in controlled environments with moderate temperatures and humidity levels.
Conclusion
Selecting the right double-sided tape for foam applications is crucial to ensure durability, effectiveness, and prevent cracking issues during use. By considering factors such as adhesive type, strength, temperature resistance, tape thickness, width, and release liner, along with proper application techniques and storage conditions, you can achieve a secure and long-lasting bond between foam and substrate.