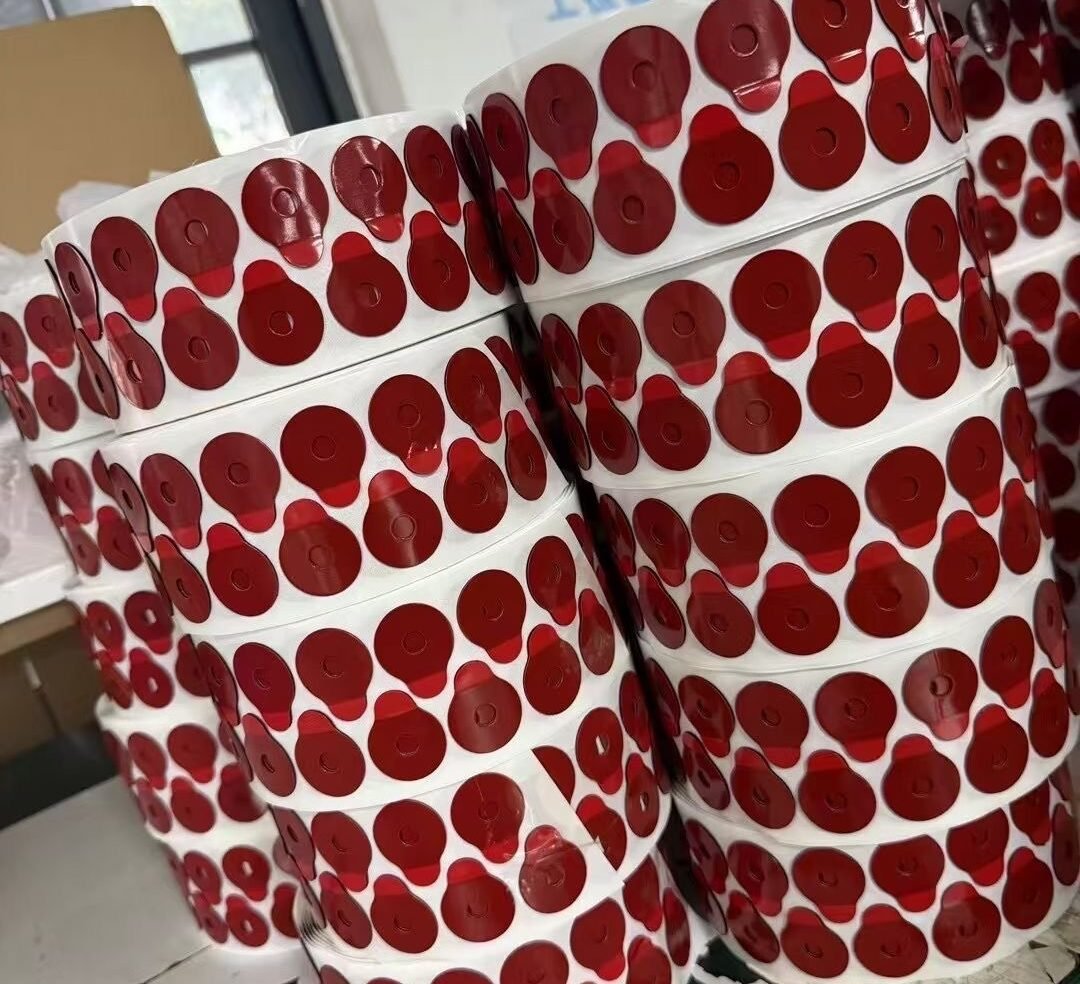
How to Choose the Right Double-Sided Tape Jumbo Roll for Industrial Die Cutting and Converting
Selecting the right double-sided tape jumbo roll is crucial for industrial precision, efficiency, and cost control. Whether for automotive interiors, electronics assemblies, appliances, or packaging, large-scale buyers must balance quality, customization, and supply continuity.
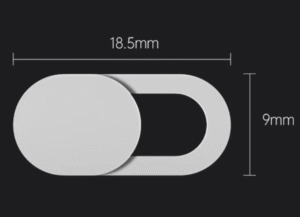
Why Are Jumbo Rolls Essential in Modern Manufacturing?
Double-sided tape jumbo rolls are supplied as large-format, uncut mother rolls, designed to be slit or die-cut to any required dimensions. Their use streamlines factory operations by:
- Lowering material costs through bulk purchasing and less waste
- Enabling custom shapes and rapid prototyping with one versatile material
- Simplifying inventory and reorder processes for multiple product lines
Real-World Insight
For instance, electronics OEMs increasingly source jumbo rolls to maximize switching flexibility on assembly lines and to reduce transport volume and fabrication leftovers.
What To Consider When Sourcing Jumbo Rolls
The right jumbo roll supplier affects both production speed and final product reliability. Key selection factors include:
1. Adhesive Consistency
Uniform adhesive coating ensures defect-free die cutting and stable bonding on final parts.
2. Backing and Liner Quality
Reinforced backings and release liners support automated processing and help prevent curl, tears, or residue during application.
3. Custom Material Options
Choose from specialized tapes—such as high-temperature acrylics, foams, or customized formulations—to meet specific job specs and testing standards.
4. Flexibility in Bulk Orders
Ensure the supplier offers quick turnaround for various roll sizes, especially when scaling up production or prototyping new parts.
5. Die Cutting & Automation Performance
Tape should withstand rapid slitting and converting without edge fray or liner splitting. Adhesive stability in demanding environments—heat, humidity, chemicals—is key for consistent output.
Industrial Case Example
An automotive manufacturing line transitioned to a jumbo tape roll solution customized for dashboard die cutting. This shift led to faster processing, less manual handling, and consistently reliable finished parts with reduced rework.
Ensuring Success: Checklist for Industrial Tape Buyers
- Is the adhesive coating uniform for precise die cut results?
- Do backing and liners support your processing speed and automation needs?
- Can material formulations be tailored for your application or environment?
- Is the supplier’s delivery window suitable for your project timelines?
- Are technical datasheets and application support available?
Enhancing Tape Converting Efficiency
By selecting a supplier with robust manufacturing processes, engineering support, and responsive logistics, industrial buyers can reduce procurement risks, improve product quality, and optimize costs at each production stage.
Conclusion: Make an Informed Tape Sourcing Decision
Industrial converting and die cutting depend on high-performance jumbo rolls that meet strict tolerance and reliability standards. Prioritize suppliers who offer technical depth, material flexibility, and consistent supply—ensuring you maintain manufacturing efficiency and scalable success.
For technical guidance or material selection support, consult with experienced industrial adhesive tape providers with a strong track record in custom converting solutions.